Frequently Asked Questions
See our Find Your Rep page.
An applicator is the assembly of parts that are designed and customized to process and crimp specific electrical terminals in a production setting. Other names for an applicator are: crimp die, tool, and crimper.
A press is a machine that operates the applicators. This is a universal machine that accommodates a variety of applicators. Another name for a press is the crimping machine.
A strip/crimp unit, also referred to as a stripper unit. It will grip the wire that the operator feeds it, make a precision cut strip length on the insulation, and then moves it to the crimp area in the applicator to complete the crimp.
Yes! There are three areas that are required for a Mecal applicator to work in another press.
- 135.80 mm shut height for press
- Tri-prong clamped base plate
- T-shaped coupling to the ram on the press
It is a good idea to have at least 1 backup set on hand in the event the tools break during production. This reduces your down time and allows you to get a new set on order from Mecal by Starn. There are no fee’s for expedited orders for emergency situation. (For emergency orders please call 814-724-1057 ext. 123 or ext. 203)
There are many factors when determining what type of applicator is best suited for a certain terminal and wire combination
- Wire Size (AWG or mm2)
- Thickness of the terminal material (in. or mm2)
- Distance between the terminals on the carrier strip (pitch)
- Type of terminal (loose piece, ferrule, multiple wire…)
- How the terminal is situated on the carrier strip (double carrier strip, end/side feed?)
Yes, Mecal engineering will take the measurements from the physical samples required with each applicator and recommend crimp specs that achieve a 17-24% compression ratio. This range with give you a tight cross section with no voids and will not damage the integrity of the components weather it be the terminal or the wire.
A Mylar tape terminal refers to the way the terminal is attached to the carrier strip. Instead of being a progressive stamping die, the terminals are attached with a heavy duty Mylar tape strip.
The pull test value is the amount of force required for the wire to be pulled out of the terminal after it has been crimped.
There are many factors when determining what type of applicator is best suited for a certain terminal and wire combination
- Wire Size (AWG or mm2)
- Thickness of the terminal material (in. or mm2)
- Distance between the terminals on the carrier strip (pitch)
- Type of terminal (loose piece, ferrule, multiple wire…)
- How the terminal is situated on the carrier strip (double carrier strip, end/side feed?)
The adjustable terminal support ensures that when the applicators ram crimps the terminal, the terminal does not get bent down or up. This ensures the terminal quality and geometrical standards after the crimping process.
The wire stop helps gauge the wire position to ensure the proper wire brush length after the terminal has been crimped. The wire stop can also be used as an ejector pin to help take the terminated wire out of the machinery.
A ferrule is a closed barrel terminal, insulated or not insulated, designed for containing the wire strands after the wire has been stripped and crimped.
This refers to how the applicators handles the excess material of the carrier strip after the terminal is removed and crimped on the wire. It will either cut it into sections or leave it as a continuous strip.
We recommend on Bench top presses the applicator to “Cut”
On automatic machines there is a hopper system that handles the scrap material, so we recommend the applicator to “Not Cut”
When properly maintained and not used in adverse conditions, the core components on a Mecal applicator can effectively last indefinitely.
When properly maintained and not used in adverse conditions, the core components on a Mecal applicator can effectively last indefinitely. We have seen applicators with several million cycles still run.
Common failure parts aside from the perishable tooling (anvils and crimp tools) would include the feed pawl and cutoff block. We have had instances where the right guide has been bent from rough handling of the applicator, though it is not common. The cutting edge of the cutoff holder will dull over time, though your technician may be able to re-sharpen the edge depending on how much material will need to be removed.
ue to how much needs to be inspected on an applicator to refurbish, we recommend replacing it. The cost of replacing the major components quickly exceeds the cost of purchasing a new applicator.
The crimp tools (dies) life expectancy widely varies depending on the terminal. On standard brass or copper terminals with tin plating, we have regularly heard tool life meeting at least 200,000 cycles. If you are working in an abrasive and/or adverse environment, crimping steel or stainless steel terminals, the tool life may be exponentially shorter. The crimp tools (upper tooling) usually need replacement before the anvils (lower tooling).
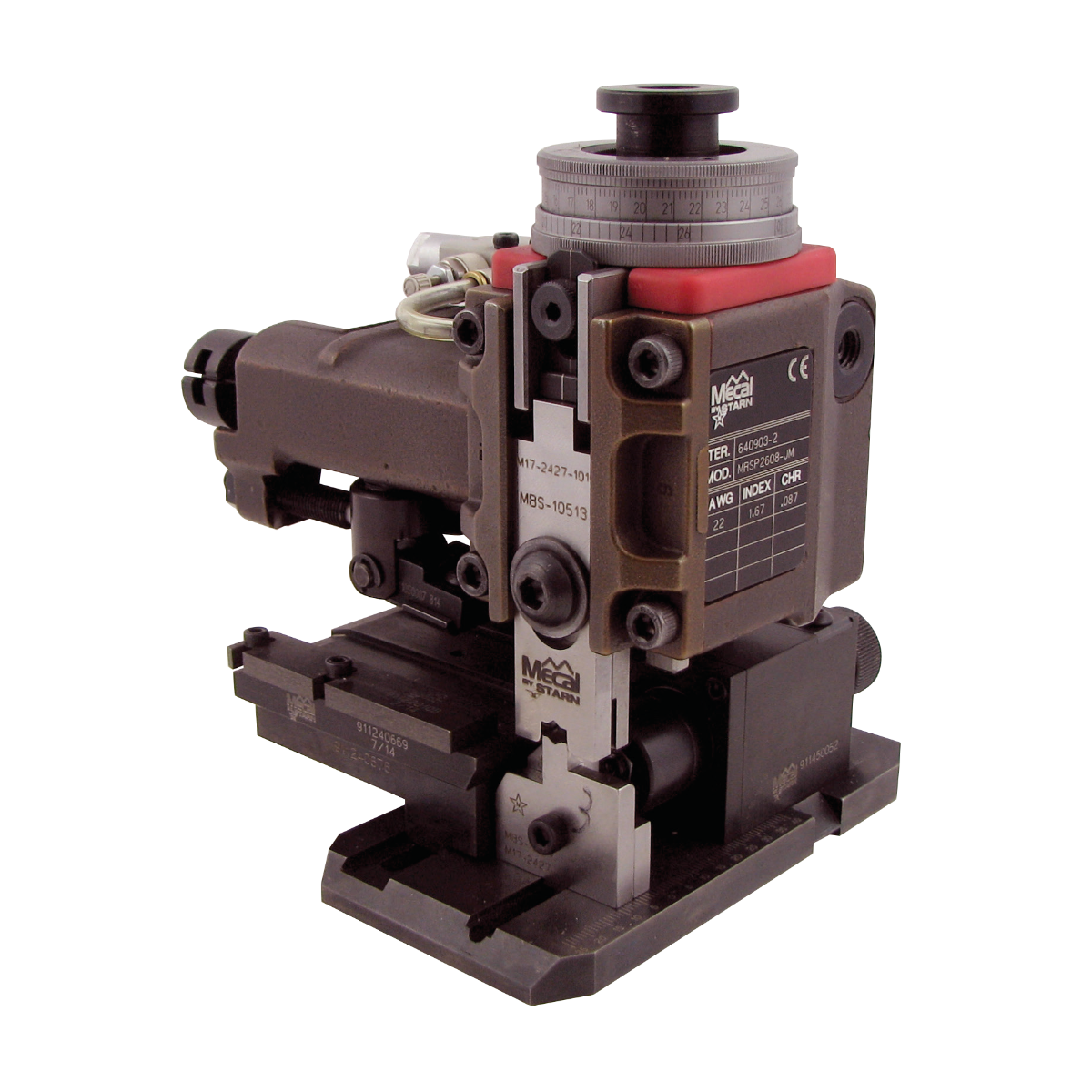
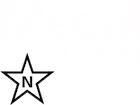
Mecal by Starn is the distributor and manufacturer of the Mecal product line in the United States and Canada.
The partnership of Mecal and Starn Tool, creating Mecal by Starn, provides world-class applicators and spare tooling for the wire harness industry. Mecal was established in 1976 with the aim of supplying the wire harness industry with the best crimping equipment available.
Mecal by Starn is a U.S. company, with a presence in almost every industry. The company specializes in wire harness crimping solutions, providing products that enable higher levels of system reliability, improved efficiency and long-term savings. Mecal by Starn serves customers in consumer electronics, automotive, energy and industrial, aerospace and defense, telecommunications, healthcare, appliance and transportation markets.
Mecal by Starn’s products and services span across a wide range of sectors, including, but not limited to, power, signal and data transmission, embedded computing and sensing, automation, connectivity and signal management. Mecal by Starn works with leading companies in virtually every industry, from IT and consumer electronics, automotive to aerospace and defense, healthcare and industrial robotics to renewable energy and telecommunications.
Mecal by Starn is known for its customer service excellence across its expansive product , as well as innovation and capability in custom-designed solutions to meet customer needs and help solve complex design challenges.
We appreciate your continued support of MBS. Please feel free to contact us with all questions or needs you have in the areas of Tooling and Components for Wire Harness Crimping.
Mecal by Starn offers 3 distinct advantages:
- Our products are the very best
- All of our customers receive world-class service
- We have 120 years of Experience